
- Optimal inspection plans based on risk
- Identify components that given its level of risk require an increased intensity of inspection (hierarchical structuring)
- Identify critical factors that impact the risk
- Establish optimal levels in economic terms pondering the effect in reducing the risk
- Systematization of the Facility/Plant
- Hierarchical structuring of risk level
- Inspection program detailed for each equipment/circuit
- Detailed description of additional activities for the reduction of risk
-
Information compilation
-
System definition - Systematization
-
Risk analysis
-
Hierarchical structuring
-
Inspection plan development
-
RBI Plan implementation
- Risk-Based inspection plan.
- Management and query of information of assets.
- Management of risk level of the facility/plant/equipment.
- Management of inspection over the lifetime of the component
-
External damage
-
Thinning by corrosion/erosion
-
SCC (Stress corrosion cracking)
-
Brittle fracture
-
HTHA (High temperature hydrogen attack)
-
Mechanical fatigue
-
Failures on equipment with lining
-
Failures on furnace tubes
- Recalculate the risk of each component included in the inspection program.
- Estimate the new frequency of inspection.
- Confirm the non-destructive testing.
- HARMI Tool. (Software to management of the inspection plans)
- Important changes which have undergone the process.
- Operating problems arising in the process since the last inspection.
- Maintenance activities or minor and major repairs performed on the outside or inside of the vessel during scheduled or unscheduled shutdowns carried out since the last inspection.
- Inspection process results
Risk Based Inspection
Risk-Based inspection is a risk assessment and management process focused on the loss of the integrity of the equipment subject to pressure due to deterioration in the material.
Benefits
Deliverables
Methodology
¿What to inspect?
Assignment of priorities for inspection according to the level of risk of each equipment or circuit.
¿Where to inspect?
Identification and location of the mechanism of probable damage (thinning, SCC, HIC, etc).
¿How to inspect?
Selection of inspection technique according to the mechanism of identified damage.
¿When to inspect?
Optimal frequency of inspection, risk level and intensity of inspection.
The systematization process consists in dividing a facility in units of study or smaller components that facilitate its analysis, the level of detail depends on the mode of the study of the Risk based inspection which is made, whether it is qualitative, semi-quantitative or quantitative.
The level of risk of each evaluated node is determined by the product of frequency of failure by the consequence of it, expressed in terms of the financial risk in $/ year
Risk = Frequency x Consequence
For specific case of RBI, risk formula is expressed as follows:
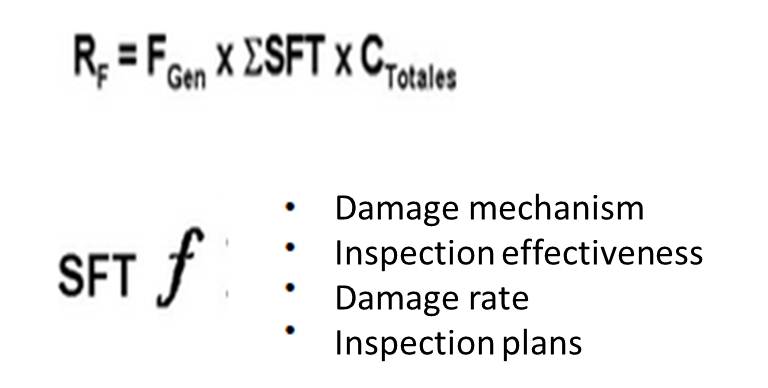
Assessment modules according to API-BRD 581,
External damage
Thinning by corrosion/erosion
SCC (Stress Corrosion Cracking)
Brittle fracture
HTHA (High Temperature Hydrogen Attack)
Mechanical fatigue
Failures on equipment with lining
Failures on furnace tubes
It is a tool for development and management of risk based inspection plans.
HARMI® has been developed on the basis of the qualitative, semi-quantitative and quantitative methodology of the recommended practice API 580 first Edition May 2002, API 581 2008 edition and the publication API-581 2000 edition
Benefits
Once completed a study of RBI requires that after of each inspection process the inspection plan is updated.
This means:
The following information is required for develop previous activities: